At the heart of Billund, Denmark, lies a building that is a veritable temple to the area's most famous creation, the humble Lego brick. It is filled with complex creations, from a 50-foot tree to a collection of multicoloured dinosaurs, all of them built with a product that has barely changed in more than 50 years.
A short walk away in its research lab, though, Lego is trying to refashion the product it is best-known for: it wants to eliminate its dependence on petroleum-based plastics, and build its toys entirely from plant-based or recycled materials by 2030.
The challenge is designing blocks that click together yet separate easily, retain bright colours, and survive the rigours of being put through a laundry load, or the weight of an unknowing parent’s foot. In essence, the company wants to switch the ingredients, but keep the product exactly the same.
“We need to learn again how to do this,” said Henrik Ostergaard Nielsen, a production superviser at Lego’s factory here in Billund.
Consumers worldwide have voiced growing alarm about the impact of plastic waste on the environment, and increasing numbers of companies are trying to use packaging materials that are recyclable or otherwise less polluting.
Coca-Cola, for instance, plans to collect and recycle the equivalent of all the bottles and cans it uses by 2030. Unilever, the consumer-goods giant, says all its plastic packaging will be recyclable or compostable by 2025. Others, like McDonald’s and Starbucks, are doing away with plastic straws in their outlets.
With so many large businesses changing their practices, recycling will “become the norm”, said David Blanchard, Unilever’s head of research and development.
Lego faces a more complex problem than other consumer businesses, though – for this Danish company, plastics are not the packaging, they are the product.
The toymaker’s highly automated manufacturing facility in Billund is a picture of clockwork. At a mammoth factory more than 500 yards long, machines arranged in rows melt plastic pellets into a molten paste and press them into moulds. A few seconds later, a batch of coloured bricks pops out, and is deposited into driverless carts, taken to be stored for shipment. Each day, the facility churns out about 100 million “elements ” – the term Lego uses for the bricks, trees and doll parts it sells.
Lego – the company's name is a contraction of the Danish words for "play well" – traces its roots back to the early 1930s
Lego – the company’s name is a contraction of the Danish words for “play well” – traces its roots back to the early 1930s, when a carpenter named Ole Kirk Kristiansen began making and selling handsome fire engines and other wooden toys.
Building system
By the 1950s, he was experimenting with plastic bricks. His son, Godtfred, began marketing the distinctive little blocks not just as toys, but as a building system that could be expanded and passed on to later generations. Bricks that date back to 1958 are still compatible with current products, according to Lego.
Today, the company sells its wares worldwide and has secured partnerships with film franchises like Batman and Star Wars to market not just themed brick sets, but movies and videogames featuring Lego toys.
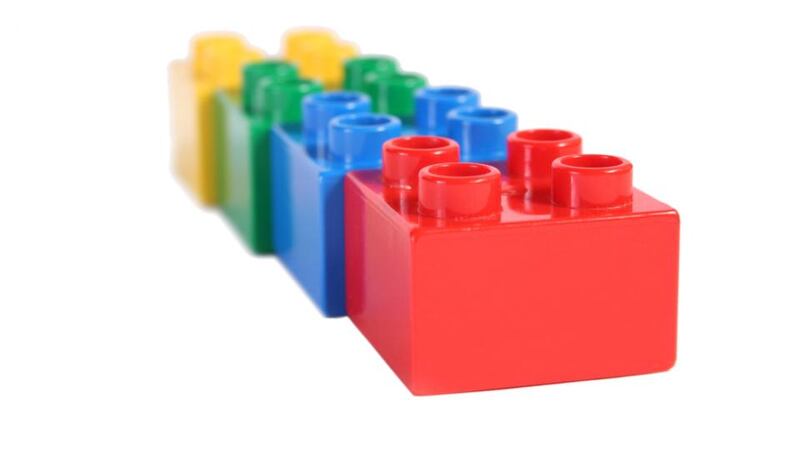
It brought in 7.8 billion kroner, more than €1 billion, in profit last year, making it larger than its US rivals Mattel and Hasbro.
But more and more children are using mobile devices for entertainment, pitting Lego not just against toy makers but against technology and gaming companies like Activision Blizzard, Microsoft and Sony. That has put the company under pressure. Lego said last year that it would cut 1,400 jobs after its revenue and profit both fell for the first time in a decade.
Its heft, however, brings with it a substantial carbon footprint. Lego emits about one million tons of carbon dioxide each year, about three-quarters of which comes from the raw materials that go into its factories, according to Tim Brooks, the company’s vice-president for environmental responsibility.
Lego is taking a two-pronged approach to reducing the amount of pollution it causes. For one, it wants to keep all of its packaging out of landfills by 2025 by eliminating things like plastic bags inside its cardboard packaging. It is also pushing for the plastic in its toys to come from sources like plant fibres or recycled bottles by 2030.
Lego is taking a two-pronged approach to reducing the amount of pollution it causes
The problem with that target, though, is that virtually all of the plastic used worldwide – including that moulded by Lego into toy bricks – is created from petroleum.
Currently, Lego mostly uses a substance known as ABS, short for acrylonitrile butadiene styrene, a common plastic also used for computer keys and mobile phone cases. It’s tough, yet slightly elastic, and also has a polished surface.
To wean itself off products like ABS, Lego has begun an exhaustive search for new, sustainable materials.
Promising materials
It is hiring about 100 people to work on these changes. Technicians methodically test promising materials to see whether they can take a whack without breaking, or survive a hard pull. They are checked to see if they withstand the heat of a Saudi Arabian summer, and take on the bright colour palette that Lego bricks are famous for. The company’s bricks may look simple, but they are made with incredible precision.
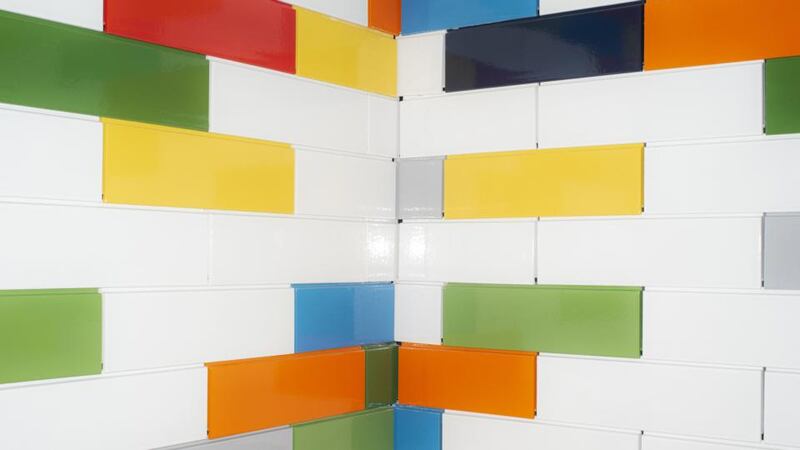
“We look at how does it look, and how does it feel,” said Nelleke van der Puil, Lego’s vice-president for materials.
Company researchers have already experimented with about 200 alternatives. Among them, van der Puil said, was a substance called PLA, one of the few bio-based plastics that are readily available. Lego is also already using polyethylene made from sugar-cane husks in flexible pieces like dragon wings, palm trees and fishing rods, but these constitute only 1-2 per cent of its output, and the material is too soft for the company’s toy blocks.
Most test materials, both bio-based and recycled, have so far fallen short. Some bricks made with the new materials have broken, leaving sharp edges that could injure a child, or have popped out with ugly, muddied colours. Others have on occasion produced misshapen or pockmarked bricks.
The search for a substitute for petroleum-based plastic could yet take years of work, Brooks acknowledges. Still, executives argue that, as a company that models itself as a de facto educator as much as a profitable enterprise, it has little option but to keep trying.
“It is important,” said Brooks, “that we can make a toy that doesn’t jeopardise” the future of children.