“I put back all the stuff that fast fashion takes out,” says Susan Owens, one of the four pioneers behind Ireland’s first studio handcrafting jeans with Savile Row-style craftsmanship and attention to detail.
Called Native Denims, it is located on the third floor of the Chocolate Factory, Dublin’s first concrete industrial building on King’s Inn Street off Parnell Street, which is now a shared creative space.
There is nothing that Owens, a master maker, doesn’t know about sewing, being one of the top machinists in the country. She started at the age of 13 as a sample machinist, and ended up as design room manager of a factory now owned by Penneys.
“Even when my three sons were growing up, I worked on the machines at home – I have never been off them,” she says, showing me around her armoury in the bright airy room with its huge metal windows, and an enormous cutting table with bolts of cloth – some 60-70 different types of denim – hanging in poles from floor to ceiling.
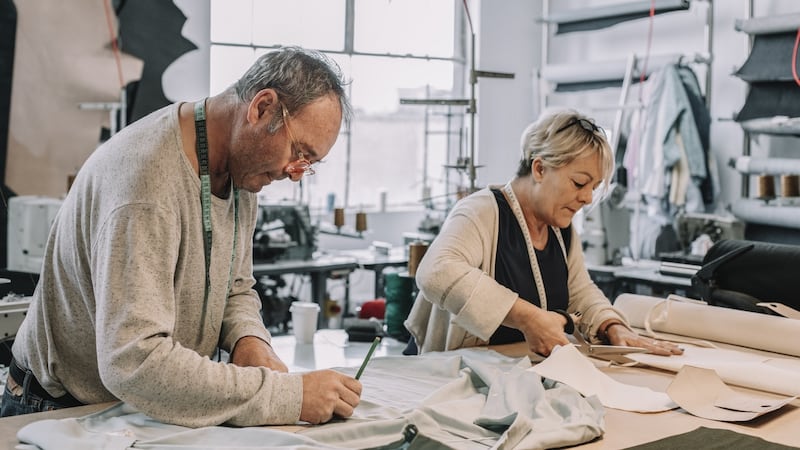
Central to it all are the complex, purpose-built machines, many of them vintage with a story of their own. There are stud, rivet and flat apparatuses, the leg hammer (for chain stitching), the beast (makes buttonholes), the feed off the arm (for twin needle stitching inside and out), the darning (“for when the arse has gone out of your trousers”), the waistband machine, the bar tacker (for closing belt loops), and the binder. “I have to be a mechanic as well,” says Owens, pointing out their various capabilities.
‘Fabric, fit and construction’
Of the four founders that include graphic artist and director of Design Factory Stephen Kavanagh and restaurateur David Murnane (of Aqua in Howth), engineer Pat O Brosnachain is the one with extensive experience of the clothing trade, who gives a masterclass in denim at the studio, showing the difference between high street jeans and their hand-crafted counterparts. He turns them inside out to compare.
“It’s about fabric, fit and construction,” he explains. On the cheap jeans, denim is “dead” as in it has no texture, pockets are shorter and cut across the grain, rivets are in the wrong places, cheap zips break, the cloth on inside pockets is flimsy polycotton, threads are lower quality, and seams and waistbands are puckered.
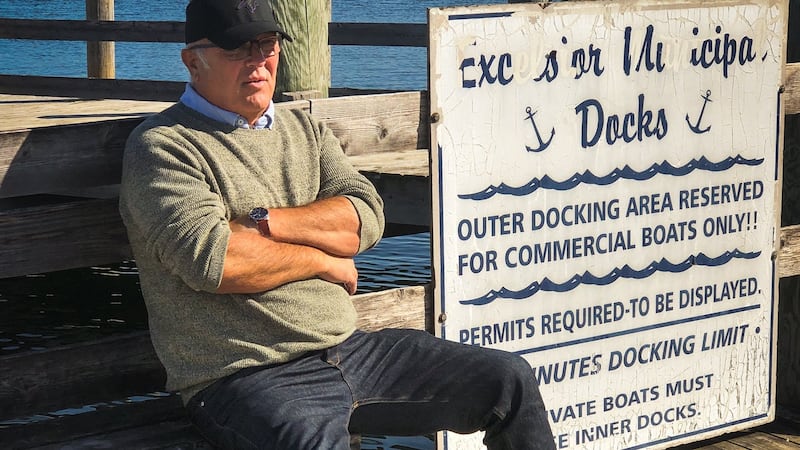
In contrast, Native Denim jeans are cut from the best cloth from around the world. There’s top end Zimbabwe cotton woven in Japan, for example; only durable Gutermann tape threads are used for the single needle stitching, and the best quality YKK zips. The jeans are made with French seams, proper waistband belt loops and tucks. Inside pockets are in heavy calico cotton and bias bound. Watching him in action and listening to his expertise and passion for the craft, it is hard not to be impressed.
He displays a pair of jeans he has made for a Turkish supplier – “our garments are up there with the best. The longer you can wear them before you wash them, the better – put them inside a pillowcase and wash at 30 degrees. We can repair within five years – we want you to wear them for 20 and the longer the better for the environment,” he says.
Sustainability
Native Denims is tapping into a trend that resonates with current thinking about sustainability, how and where clothing is made and its environmental impact. The initiative of these longstanding friends, two of whom went to the same school, was prompted by an article in Drapers about the revival in the UK of premium denim jeans due to a growing number of consumers who want to buy less but better.
“Jeans have a long history in Ireland and were made here for decades,” O Brosnachain points out, showing me a pair made in Ardee for Lee Jeans. In addition, the expertise that is brought to making jeans from denim also applies to making them from moleskin, a heavy-duty cotton – I am shown one in army green. Their “mother” brand is called John Ireland, which was an Irish company on Ellis Quay established in 1834 (it used to make Garda helmets). Native Denims is their denim range and the beginning of what they hope will be further clothing developments.
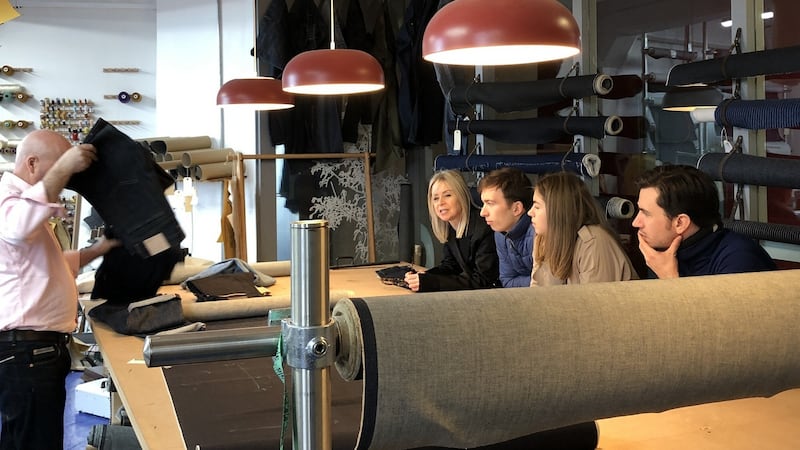
So, what do these high-quality handmade jeans cost? They have three offers: a basic stock jean for €160 (from pattern block variants on standard sizes, with free repairs for five years), a customised jean (where customer chooses fabric, threads, rivets, selvedge, etc ) for €250, and the bespoke jean (where the customer has his or her own pattern block specially made) from €500.
“Fast fashion is a race to the bottom,” says Owens. “We are the complete opposite. We have gone back to the way jeans were meant to be made.”
Riveting stuff.