Weight. Mass. Heft. Bulk. As anyone who has ever had to join Weight Watchers or shop at High, Wide and Handsome knows, it’s the enemy. The more that you pile on, the worse it gets, and the more strained become the buttons on your shirts.
With cars, weight is just as bad and arguably an even more serious issue. You or I, with a bit of discipline and a bag of carrots, can lose some of our physical mass. For a car, it’s baked in from the beginning, and every kilo adds to a destructive downward spiral.
The heavier a car is, the more power it needs from its engine or electric motor and for its batteries to move around. That triggers a need for bigger, more efficient cooling systems, more fuel or more batteries to provide that power. They also need bigger wheels and tyres and heftier brakes to keep all of that on the road.
All of which adds weight, which needs more power. It is the rocket scientist’s infernal equation – you need more power, which needs more fuel, which means more weight, which means you need more power.
The lighter a car is, the more efficient it will be. It will use less fuel or consume electricity at a slower rate, which means it can either go further on a single battery charge or go the same distance as a heavier car but with a smaller, more efficient, lighter and, crucially, cheaper battery.
Carbon fibre
We’ve known for years how to take the weight out of a car and it’s called carbon fibre. A composite material, it has been used in racing cars since the 1970s, and in aviation before that. Moulded and set in a resin, carbon fibre can be formed into any shape and is stronger than steel, but at a third of the weight for an equivalent strength. It’s how Formula One drivers can now walk away from horrifying accidents that would have claimed the lives of their predecessors in the 1960s and 1970s.
McLaren, diversifying from its Formula One activities, introduced an all-carbon chassis to road cars in 1992, with the F1 supercar. While tremendously light and efficient, it was also staggeringly expensive – $1 million (€820,000) back then – and carbon construction hasn’t become much more affordable in the interim.
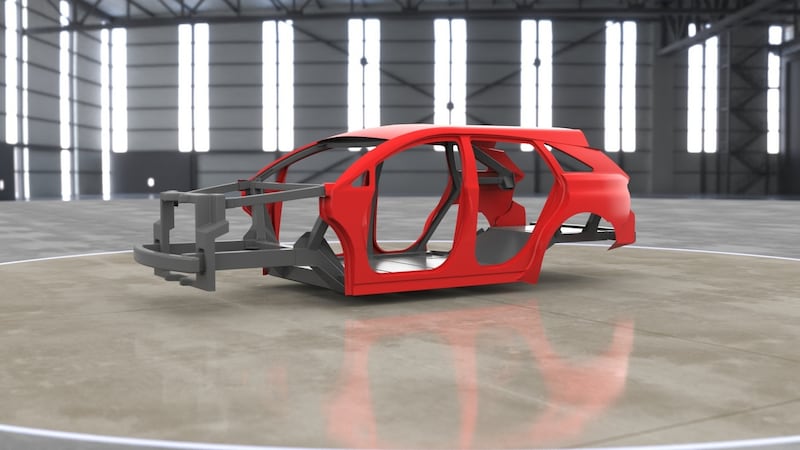
BMW thought it had made a breakthrough in the early 2010s, but its i3 and i8 electric and hybrid cars, built around a supposedly affordable carbon structure, still proved expensive to make and required a new factory in which to be built.
Plasan, an Israeli company, now reckons it has cracked the code of making an affordable carbon-fibre structure, and one which can, in theory, be integrated into an existing car factory and used alongside existing car-making techniques at mass-market level. Plasan is estimating that its new carbon-composite car structure is 45 per cent lighter than an equivalent steel vehicle and 20 per cent lighter than an aluminium car. And it all started with armour plate.
Armour plate
Since it was set up in 1985, Plasan has been in the business of making armoured vehicles, sold to armies and police forces worldwide. These days armour is not about battleship-style thick sheets of steel plate, it’s about light and flexible composite materials – Kevlar and carbon fibre.
Nir Kahn, Plasan’s design director, was keen to push the company further into road-car development and away from military products. Plasan had bought out a composites maker in the United States to fulfil a US army contract and had inherited a division that makes panels and parts for the Chevrolet Corvette in the process. It was this that sparked Kahn’s idea for a full, lightweight but affordable vehicle structure.
“We were experimenting with ways to do bulletproof armour that was structural, built into the vehicle, rather than bolted on afterwards,” Kahn tells The Irish Times. “We realised that what we had created was just one product bonded to another, so we had to go back and go for the holy grail to see if we could make a structural composite material cost effective. And if we could do that, then we could forget about armour, which is of course quite a small market, and move into the automotive market.”
Cost was the key. Making composite structures is a well-known process, but because it was born out of aerospace and motor-racing technology, it’s both labour-intensive and expensive – two things that no major car company wants to hear about a new technology. Kahn’s priority then was not the ultimate tech, but the best tech for the best price. “It isn’t about shaving off the last gramme like they do in motor sport,” said Kahn.
“It’s about how much cost you’re adding for each kg you’re saving. That is the metric to focus on, and it needs to be under $10 per kg saved to start being attractive to mainstream car manufacturers. By contrast, aeroplane manufacturers consider a $1,000 premium per kg saved to be a good deal.”
Pultrusion
Plasan and Kahn’s innovation was a process called pultrusion. Extrusion is a process well understood and widely used in the car-making world. Take a lump of lightly molten aluminium, squeeze it through a die, and it will come out in the shape you need, which can then be bonded and riveted to the structure of your car.
Pioneered by Lotus in the 1990s, aluminium extrusions are now widely used. What if you could do the same with ultra-light carbon fibre? Instead of pushing it through a die, a pultrusion structure is pulled through, and its shape and the number of fibres in it can be varied along its length once it maintains a consistent cross section. “It can be a matt or a weave or basically any kind of textile, and you can decide where in the mould you’re pulling it through,” says Kahn.
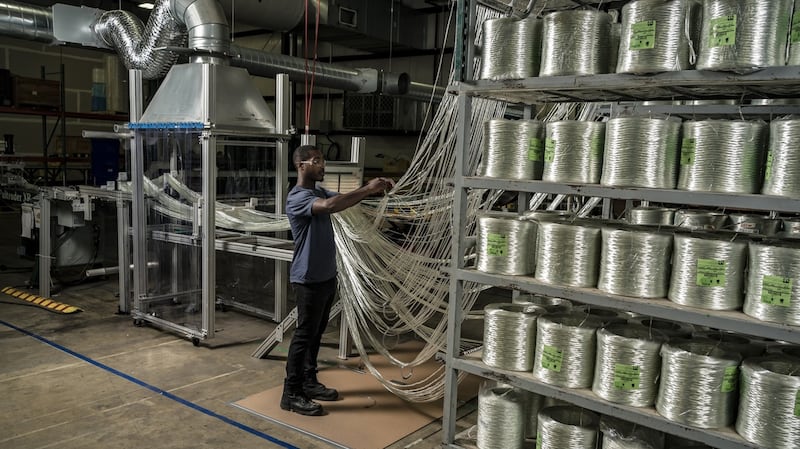
“So you can vary the strength across the structure and you can have any kind of fibre you like, even fibre-optic cable – so if you’re doing an electric-car chassis, you can do it with cooling and communications wiring built into the structure. You could even have sensors that detect any damage to the batteries or the bodywork wired in.”
Easy assembly
Plasan then developed aluminium nodes that attach to each finished composite section and allow them to be quickly and easily assembled into a finished structure. The beauty of which is that it could, potentially, be easily integrated into existing vehicle production lines with no need for massive, expensive factory refits or new-build greenfield sites.
“One of the fundamental things that allows car factories to knock these things out is that they’re essentially dropping layers on to one another,” Kahn says. “There’s very little what you might call meticulous inserting, it’s more throw something down, throw something on top, and [. . .] weld it together. With our structure, it’s slightly different from a welded-steel production line obviously because there is no welding. But even then there’s very little difference, you’re basically just replacing the heads of the robots.”
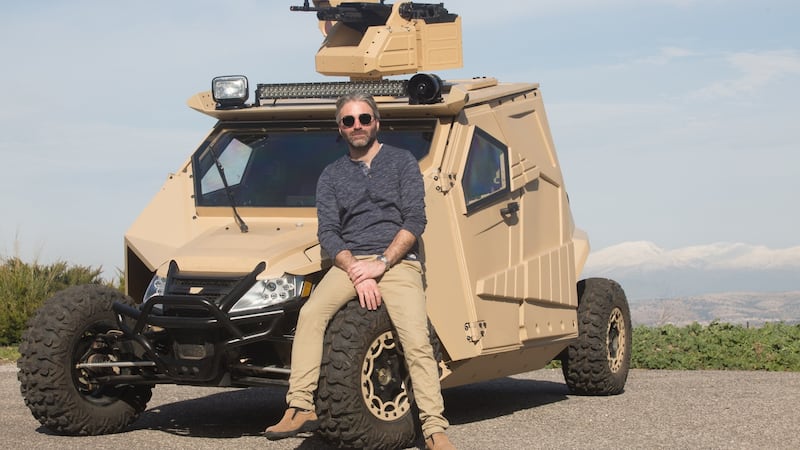
“The robot doesn’t care what the part’s it’s working on are made of; it places the parts in exactly the same way and the only real difference is that instead of coming in with a spot welder, you’re putting a bead of adhesive down and riveting the structure together. It’s what Audi’s already doing, it’s what Mercedes is already doing.”
At Plasan’s current anticipated cost of about $10 per kilo reduction, the tech is still a little costly for the cheapest models on the road. You’re unlikely to see it just yet in a Fiesta or a Polo. But for a medium-priced car, a BMW 3 Series for example, it’s entirely doable, and the potential benefits from making a popular vehicle lighter by half, especially now that the bulk and heft of electric car batteries have to be taken into consideration, could be profound.
A car that’s lighter is more efficient, not only in terms of energy consumption – whether liquid fuel or electricity – but also in terms of having fewer secondary emissions of particulates from brakes and tyres.
Innovation based on military tech is nothing new in motoring – we drive SUVs today because the Willys Jeep helped to win the second World War – but this “lightweighting” technology could be a sword turned to ploughshare in the fight against climate change.